
Accidents during Mooring Operations
Loss Prevention Bulletin
The Club’s analysis of significant claims found that approximately 5% of all severe personal injuries happened during mooring or towing operations.
(Loss Prevention Manager, West P&I)
Although a substantial proportion of these claims resulted from slips, trips and falls, almost half were caused by parting lines or involved crewmembers’ failure to abide by safe working practices whilst handling lines. The invariable aftermath of these incidents resulted in lifechanging injuries as well as emotional trauma being suffered. In response to such accidents, this bulletin has been written to reemphasise correct procedures and promote good practice.
General
Routine precautions should include regular checks of the deck areas used for mooring operations. Unless already fitted with treads, mooring decks’ surfaces should be treated with antislip paint and must be kept clean and free of clutter. Mooring winches and deck fixtures and fittings should be inspected, maintained, and greased according to the vessel’s Planned Maintenance System (PMS) requirements. In particular leaking joints in hydraulic lines should be rectified, possibly considering the construction of save-alls to protect the decks from further leakage.
Fairleads and rollers should be regularly lubricated, checked for free movement, examined for wear, and bitts examined for distortion and fractures. Leads that have previously been used for wires should be inspected for metal damage before being used with fibre ropes. Winches must operate and stop smoothly and be isolated after use.
Directions of movement should be clearly marked. Winch brakes maintained in good order, with all linkages working satisfactorily and adequate brake lining thickness per the manufacturer’s instructions. Winch drums are designed such that they are most effective at holding a rope under tension when the line is pulling against the fixed end of the brake band arrangement. Therefore, it must be ensured that lines are wound onto drums according to the manufacturers’ recommendations to ensure the brake does not fail prematurely.
On winch drums fitted with disc brakes, ropes can be wound onto the drum in either direction. Regardless of type, winch brakes should be set to render at approximately 60% of the Minimum Breaking Load (MBL) of the rope on the drum. Clutches should operate smoothly, and clutch control lever securing pins fitted ready for use. Drum ends should be smooth, clean, and free from grooving damage, rust, paint and oil. Before mooring operations commencing, all winches, ropes, fixtures, and fittings should be visually examined and machinery tested; any defective equipment should be taken out of service and repaired or replaced before use.

Care of Ropes
Unless proper care is exercised to preserve the condition of a line, its tendency to break under tension may increase significantly and reinforces the necessity for a comprehensive Line Management Plan (LMP) to be implemented. When considering the rope care protocols to be carried out onboard, integrating the manufacturer’s instructions and recommendations into the vessel’s PMS is a vital component of the process.
Fibre Ropes
Almost all fibre ropes in use at sea today are manufactured from synthetic materials. Mooring lines are often made of polypropylene, polyester or high modulus polyethylene (HMPE). Different synthetic materials have unique properties; HMPE, for example, is resistant to most chemicals but will melt at a lower temperature than polypropylene; therefore, the synthetic fibre ropes’ unique properties in use onboard should be known and appropriate precautions are taken.
Ultra-violet rays may result in actinic degradation, and coils of synthetic ropes should always be stored away from direct sunlight when not in use and covered when in port. The ropes should be stowed well away from paint, thinners and chemicals as these substances’ vapours may also cause damage. Storage areas should be well ventilated and fitted with wooden gratings or pallets to assist drainage and improve air circulation. Ropes should never be stowed against hot bulkheads.
A visual inspection of synthetic ropes
should be made at frequent intervals,
including a thorough examination of
the inner strands and the condition
of the splices. “Powdering” between
strands is usually an indication
of excessive wear and weakness.
Excessive surging from warping drums
or bitts should be avoided as friction
may cause the fibres to fuse, resulting
in a reduction in strength. The fitting of
eye splice protectors around rope eyes
may provide additional protection
against wear. When the working end
of a rope, be it on a winch drum or a
loose coil, becomes worn or damaged,
it should as a temporary measure be
either be cropped and re-spliced or
the rope “end for ended”.

Wire Ropes
With the correct lubricant grade, lubrication should be carried out regularly to minimise internal and external corrosion, and cores must not be allowed to dry out. A kinked wire will reduce strength; therefore, care must be taken to avoid bending it excessively. Similarly, crossing wires on the drum end may cause the line to become crushed or flattened. The presence of snags, kinks, bird caging, crushed or flattened strands, and corrosion reduces the wire’s strength. Wires, including splices, should be periodically examined along their entire length and any damage evaluated in line with the company’s wire discard criteria, which should be detailed in the vessel’s Safety Management System (SMS), to determine whether replacement is necessary. If a wire’s strength is in any doubt, it should be taken out of service and replaced. When handling wire ropes, suitable gloves should always be worn to protect the hands from snags.
Parting Ropes
When berthing, the most critical period is often after the first line has been sent ashore. The strain on a single line may be considerable, significantly increasing the risk of its parting. Although synthetic ropes have great elasticity and an excellent capacity to absorb sudden shock, breaking when under stress may produce a potentially dangerous snapback. It is difficult to predict when a synthetic rope under strain approaches its breaking point as audible indications are often absent. Personnel on the mooring deck should always stand in positions of safety in such circumstances, clear of the snap-back zone area.
Wire ropes have less elasticity but
may give a prior warning if about to
part. Sharp cracks may be heard, and
individual strands may begin to unravel
before the breaking point is reached.
Although a parting wire may not travel
as far as a synthetic rope, snap-back
effects can be equally harmful. Even
when fitted with a synthetic fibre rope
tail, wire rope’s limited ability to absorb
shock makes it desirable that only fibre
ropes are used as first lines to heave a
vessel alongside.
Whenever a line is observed to be
coming under excessive strain, all
possible measures shall be taken to
reduce the line’s tension so far as is safe
and practicable.
Stoppers
Stoppers should always be of the same type as the fibre rope to be held, of sufficient length and adequate strength; ideally, 50% of the MBL of the line being held.
Synthetic ropes demand flexible synthetic stoppers made of low-stretch material and with a high melting point. Polyester and polyamide stoppers are both acceptable; however, it is advised that polyamide stoppers are not used with polyamide ropes due to its low friction of coefficient. The stoppers should preferably be rigged with both ends free so that they crossed over and under, “West Country” method can be used.
Chain stoppers should be used with wire ropes, first fastening the chain in a well-spaced “cow hitch” and turning the tail several times against the lay of the wire. It must be remembered that stoppers serve only to hold the line momentarily while it is secured, and sudden shocks or increased load may cause the stopper to part. Once a rope has been laid up on the bitts, Loss Prevention Bulletin the stopper must be removed from the rope. When a line has been tensioned on a drum end, it must be stoppered and transferred to mooring bitts; it is bad practice to leave lines on drum ends that are not in the process of being tensioned or slacked
Mooring Operations
It is essential that sufficient personnel are detailed to attend the mooring operation and that the activities to be undertaken are adequately explained and supervised by a deck officer. Personnel not involved in the mooring operation should be kept well clear of the mooring decks. In the event of an unusual or non-standard mooring operation, it is recommended that a new risk assessment be completed before the operation commences as they will potential have associated hazards not covered within the risk assessment done for a standard mooring operation.
The officer should take charge of the communication link between the mooring deck and the bridge. All communications should identify the vessel to ensure that no misunderstandings occur when other vessels communicate on the same radio frequency. Accurate reporting to the bridge is essential, with instructions from the bridge acknowledged, repeated and then confirmed once actioned. The bridge must also be advised when all ropes, be they moorings or tugs lines, are clear of the water and main engines and thrusters can be used.
Additionally, there must be a clear communication line between the mooring officer and the linesman, and parities must always maintain visual contact during the operations. There should be one linesman who is clearly identifiable as the contact point to which visible/hand signals are communicated. The mooring officer should not get involved in the physical mooring activities but should maintain an overview of the operation. Keeping a sharp lookout for potential hazards should be considered an integral part of the mooring officer’s duty.
The officer should also ensure that the mooring party wears correct personal protective equipment in line with the requirements of the vessel’s SMS, which will include, as a minimum, safety helmets (with chinstraps secured), appropriate footwear, and high visibility clothing which will not become entangled during mooring operations. Safety goggles should be available if an anchor needs to be used, and gloves should be used whenever wire ropes are handled due to the danger of injury from broken wires. Provided permission has been obtained from the bridge, mooring decks should be illuminated at night.
Split drum winches are designed so that the line should leave the drum’s tension side from the first wrap of rope to ensure maximum holding capacity. Care must be taken when crewmembers are transferring the rope from the drum’s storage side to the tension side; the rope should be pulled through the gap in the drum divider rather than pushed, as it may spring back and strike the crewmember.

Self-tensioning winches are fitted on some vessels; however, it is recommended that these are not used in self-tensioning mode when a vessel is connected to a shore manifold or has limited room ahead/or astern of the vessel. There have been many instances of vessels, when using self-tensioning winches, creeping along a berth due to the prevailing environmental conditions.
The responsible officer should also make sure that the basic principles of safe mooring are closely followed by those working under their direction by ensuring that, as a minimum, the following points are abided by whilst they are conducting mooring and towage operations:
- Never stand within the bight of a line.
- Never stand in the bight formed between the winch drum or the drum end and the fairlead.
- Always stand in a position of safety, clear of a line’s snap-back zone area when lines are under tension. Lines will generally snap-back in a direction based upon the direction in which it was leading. When led around pedestals or bitts, the line will snap-back around these in a much larger arc.
- Ensure only experienced crewmembers operate winch controls.
- Never leave rotating winches unattended or with winch control levers tied off.
- Ensure winch operators can see the officer in charge.
- Always try and remain in full control of a line.
- Never attempt to stop an unchecked line by grabbing hold or stepping on it.
- When lines are being run using a line boat, the lines are to be lowered under control to the boat and are not to be let go such that they fall uncontrollably into the boat/water.
- Avoid large changes in the direction of a line by leading ropes and wires around sharp bends.
- Don’t surge lines unnecessarily; always endeavour to winch back.
- Avoid crossing wires and synthetic fibre ropes or leading both rope types through the same fairlead.
- Don’t stand too close to the drum end when heaving or slacking.
- Ensure that a second person helps each drum-end rope handler pay out the line or pick up the slack.
- With synthetic lines, don’t apply too many turns to the drum end. Three or four turns are generally sufficient; however, whelped drums may require more turns.
- All leads within the mooring line arrangements must be of matching dimension, MBL and material. Where synthetic fibre and wire ropes are available, the two types should not be mixed in the same service. For example, breast lines should not be a mixture of wire and fibre ropes; instead, they should be either wires or fibre ropes.
- Ensure that during the running of the mooring lines that each service, i.e. breast, spring, head and stern lines, are done as stipulated in the Towing and Mooring Arrangements Plan and symmetry about the vessel’s longitudinal centre line is maintained as much as possible.
When making fast to a tug, in most cases, a tug’s line will be used, however; if a ship’s line is required to make the tug fast, then care should be taken to select the best ship’s line available, ensuring the line is in good condition, has sound splices and does not have short splices within its length. The ship’s line selected should be of sufficient strength to withstand any dynamic loading imparted in it during the towing operation. It is recommended that the MBL of the ship’s line’s line is at least twice the bollard pull of the tug. When connecting or letting go towing lines, either provided by the tug or vessel, these must always be kept under control, using messengers to heave or slack the line as necessary.
Following any tow line connection, all mooring personnel should stand well clear of the operational area as tension in the towing line often increases rapidly and with little or no warning. When needing to work within the operating area or to attend to the tow line, always keep clear of bights of rope and the towing line’s snap-back zone area.
The eye of a tug’s towing line should
be placed over a mooring bitts post
clear of rope or wire, and ship’s lines
laid up on the bitts. Bitts should be
prominently marked with their safe
working load (SWL), and the SWL of
bitts used for towing must exceed the
expected dynamic loadings in the tow
line.
Tugs should only be cast-off after receiving instructions from the bridge and never on the tug crew’s orders.
Associated Loss Prevention Bulletins on the topic of mooring operations which can be seen in the listed publications below:
- Snap-Back Zone.
- Monkeys Fists on Heaving Lines - Use of Inappropriate Weighting Material
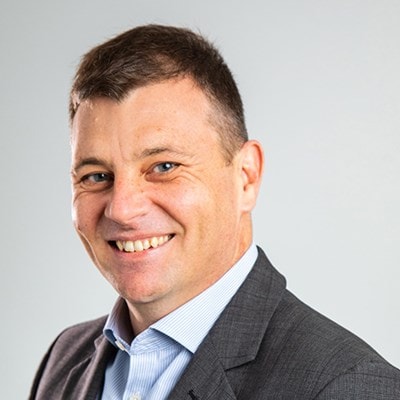
Dean Crossley
Loss Prevention Manager
T +44 20 7716 6059
E Dean.Crossley@westpandi.com
Dean is the Loss Prevention Manager at West P&I's London Office. He is a Master Mariner with seagoing experience on a variety of dry cargo vessel types. Before joining the Club in 2016, upon transferring to shore-based employment, for over 13 years, Dean has worked at an IG P&I Club in London as a Claims Manager and as a Marine & Warranty Surveyor at leading marine consultancies